Oakley Fifth Avenue
Oakley Fifth Avenue, New York City
Zahner worked with Oakley’s architectural team to create the new Oakley flagship store on Fifth Avenue in Manhattan, New York. The project’s scope included the development of a geometric facade with no visible fasteners, which could be installed on a 100-year-old building across one of the busiest streets in New York.
This wasn’t Zahner’s first collaboration with Oakley. In the late 1990’s Zahner’s engineered metal-fabricated systems were used the facade and interiors of the Oakley Headquarters in Foothill Ranch, California.
For the Oakley Flagship at Fifth Avenue, the company’s unique ”Mad Science“ aesthetic shows through as a massive black geometric facade and canopy system for their latest retail experience.

Oakley Fifth Avenue in New York City.
Photo © A. Zahner Company.
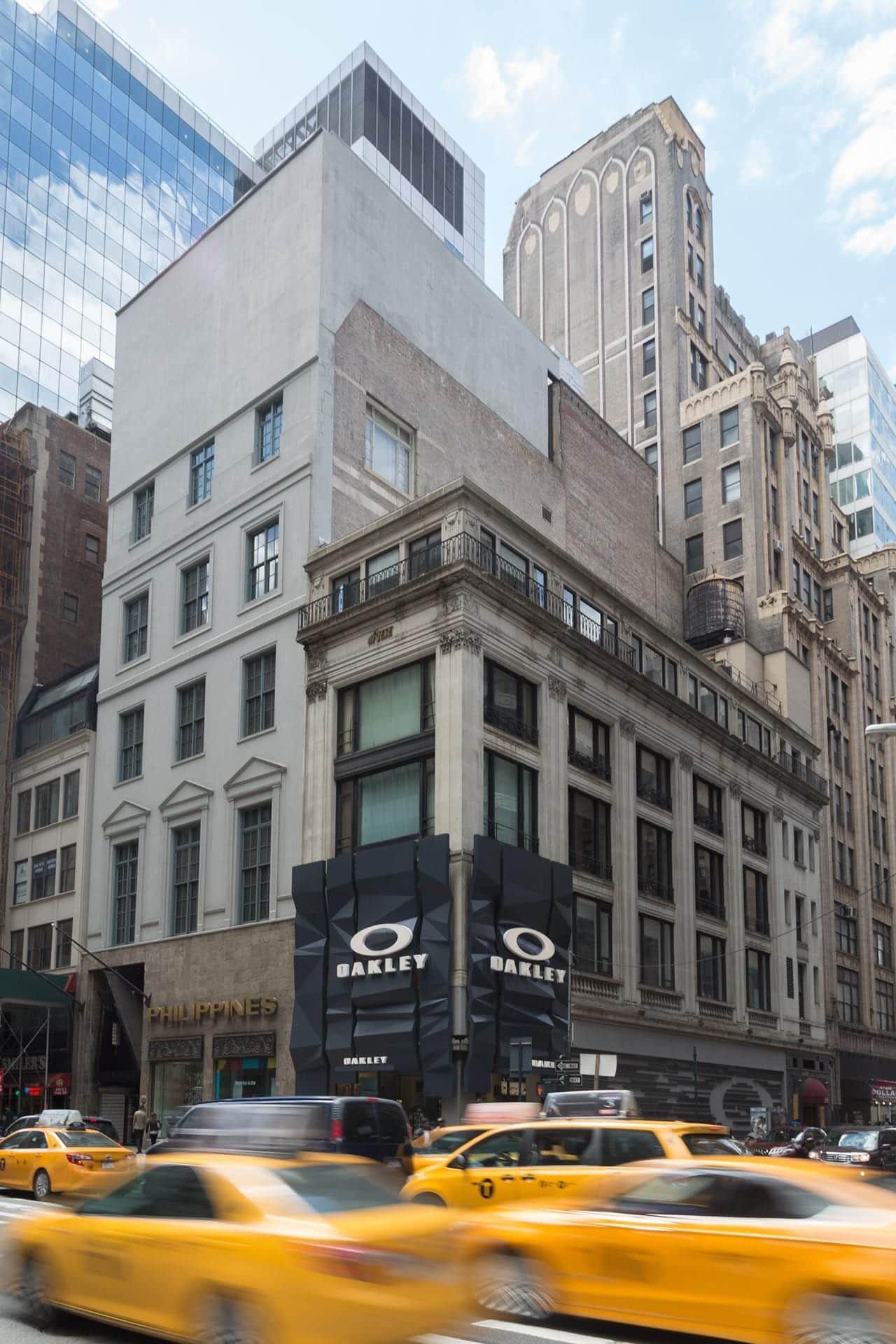
Oakley Fifth Avenue in New York City.
Photo © A. Zahner Co.
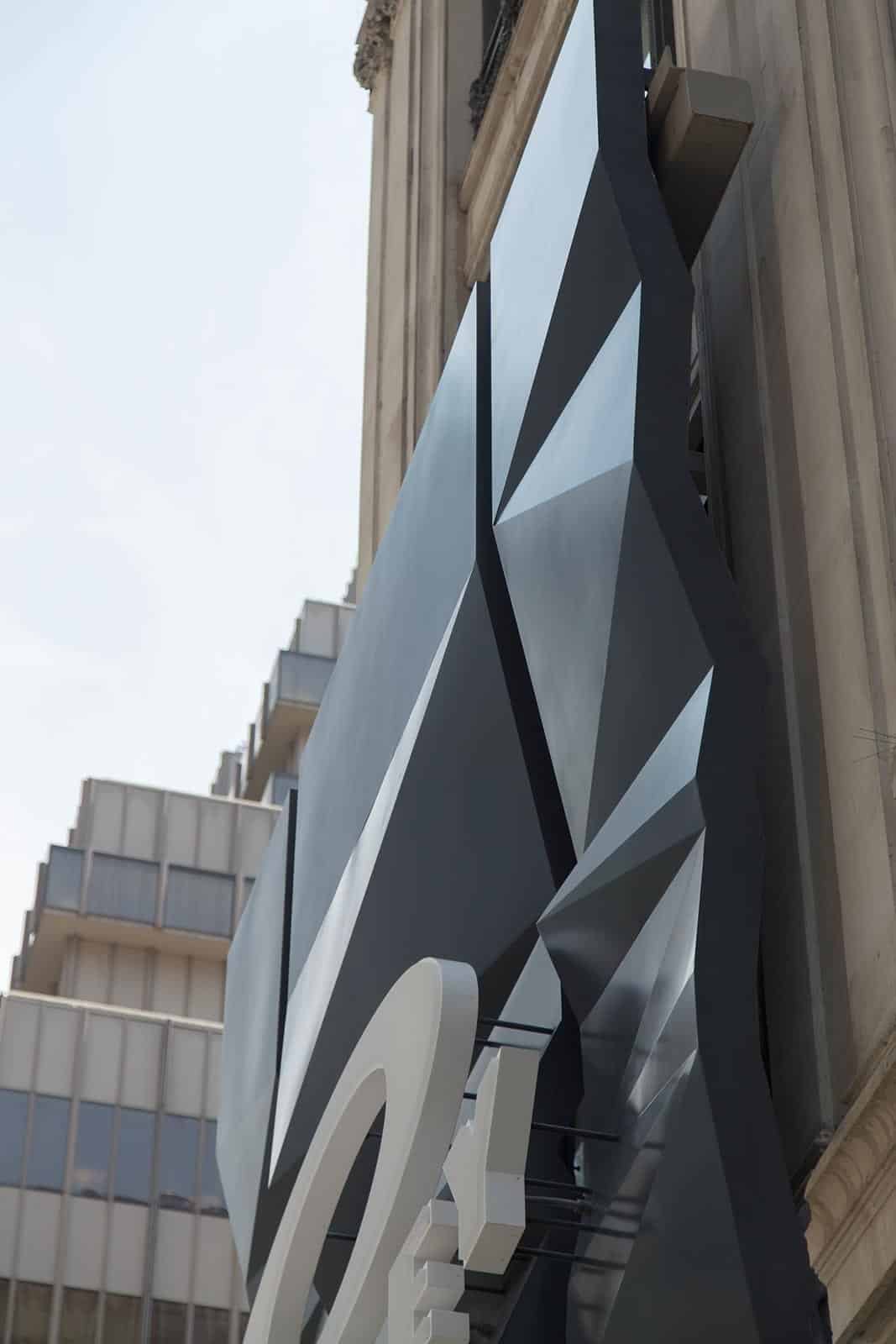
Details of Oakley Fifth Avenue in New York City.
Photo © A. Zahner Company.

Oakley Fifth Avenue in New York City.
Photo © A. Zahner Co.
Developing the Design for the Oakley Flagship on Fifth Ave
One of the design challenges for this project, was that the client didn’t want to show or see any fasteners on the surface of the system. Zahner engineers and fabricators rose to the challenge, providing a connectionless facade.
The aluminum skin used Radius Reduction technology to create the geometric forms. These angular forms were v-notched using a custom milling system developed by Zahner for making a v-groove on unique panels. On this system, each of the holes were cut, as well as the perimeter shape for the forms. Each panel had ten to fifteen skins in 3/16″ aluminum, with 3/4″ steel structure. The finished surface was painted with acrylic polyurethane coating system, spray-applied with Matthews System paint. The design has 8″ between the panels.

Architect’s renderings of the Oakley Facade for Fifth Avenue Flagship.
Rendering courtesy of Oakley.
The existing building is more than 100 years old, which created unique hurdles for attaching a heavy load. Zahner project team coordinated steel, and coordinated the site, for three months while developing the model. During this process, the design team discovered code changes providing additional challenges. The offset couldn’t go more than 18 inches off of the building. Some of the pieces were canopies, so there were limitations on how far off the building it could go.
As part of the project’s Design Assist phase I, a mockup was made of the design. This mockup was displayed in Kansas City for the clients, which provided valuable feedback for the fabrication of the final product.
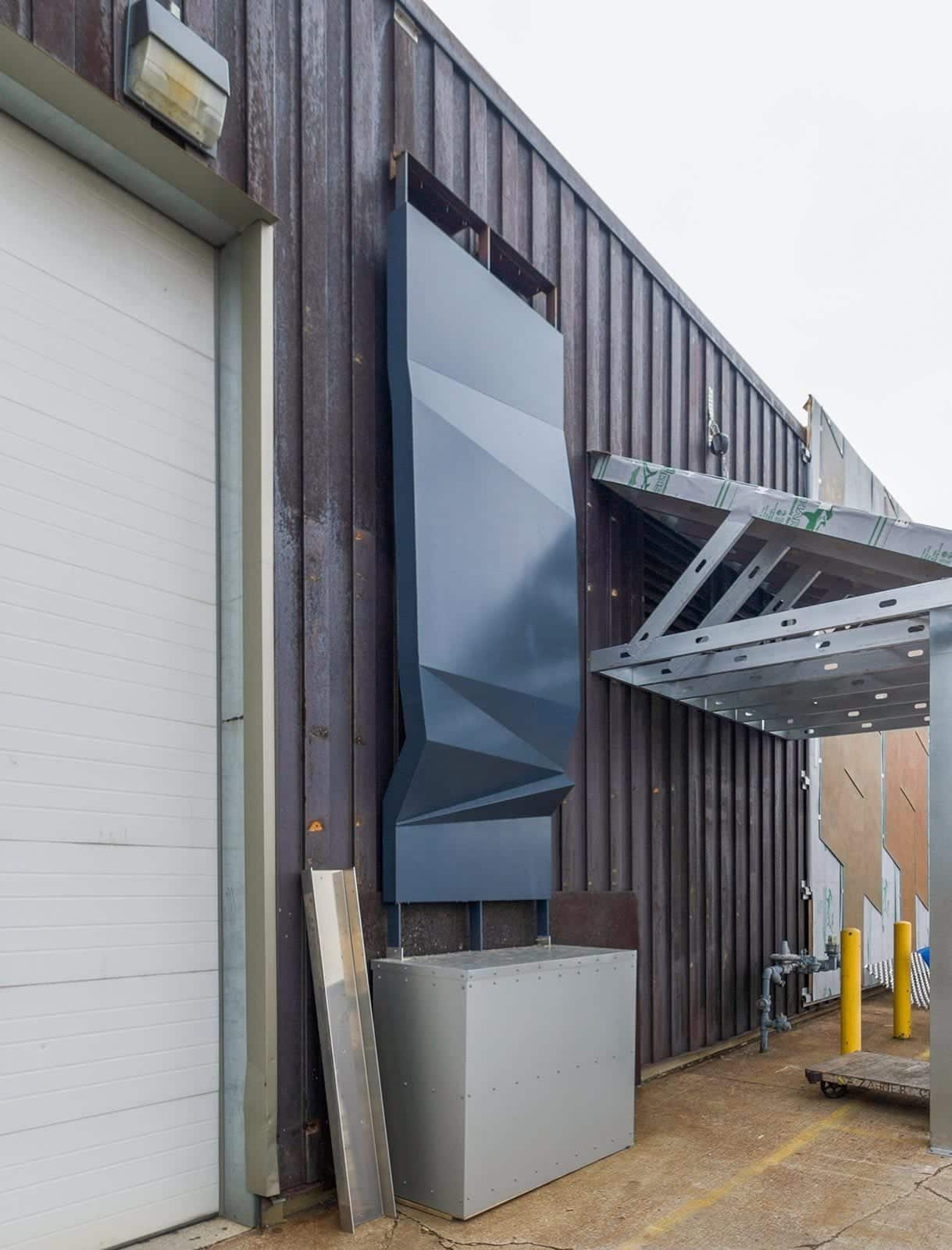
Mockup at Zahner in Kansas City for the Oakley Fifth Avenue in New York City.
Photo © A. Zahner Co.
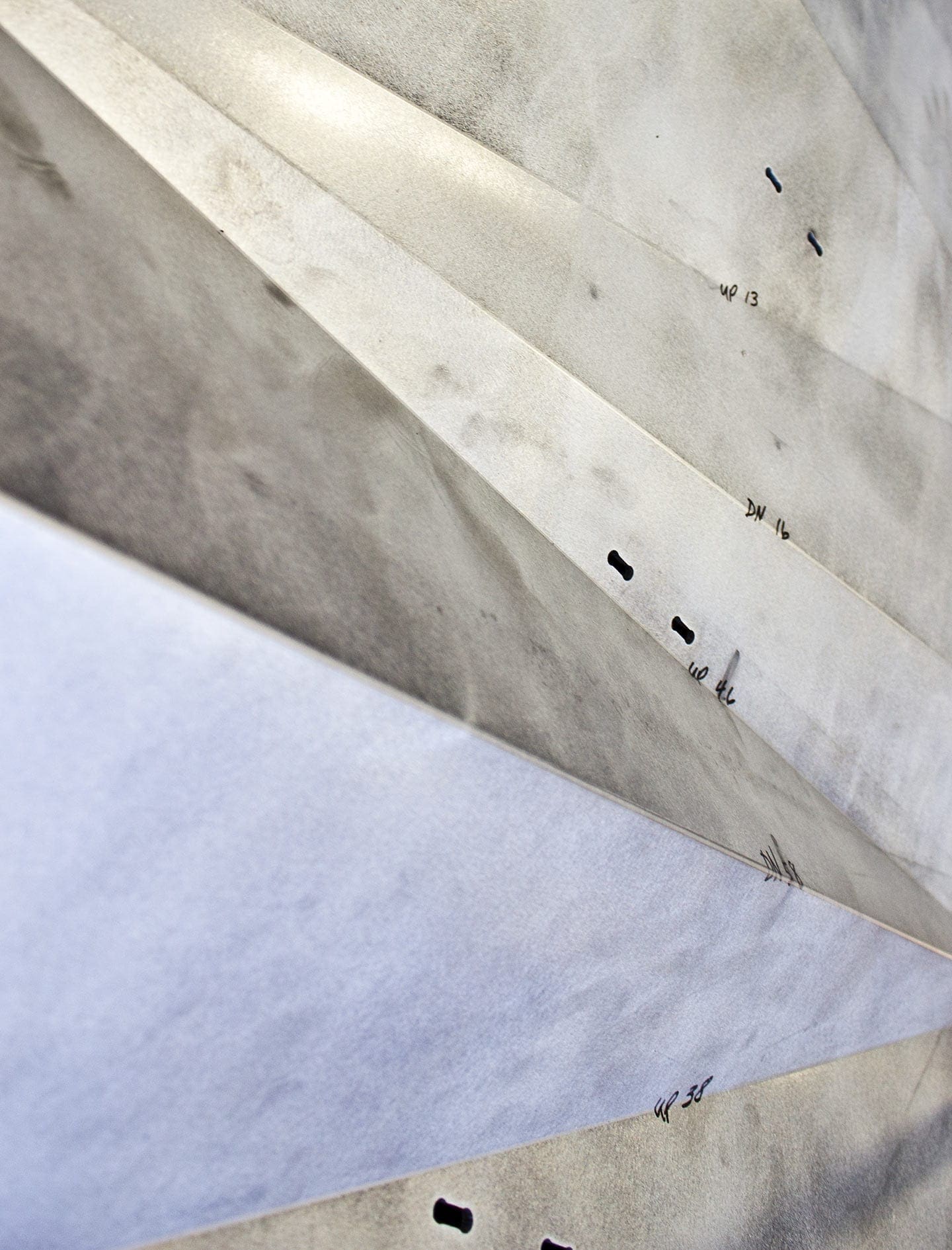
Aluminum profiles with notches cut for clips.
Photo © A. Zahner Co.
Making the most efficient installation possible.
The large elements were to be hoisted on one of the busiest avenues in Manhattan. So providing The design was essentially three sections: the steel structure, the aluminum clip, and then the aluminum skin. The clip had all the intelligence. As such it is a very smart object. The connection between steel and aluminum facade, is a clip connection.
There is no mechanical connection operation required in the field. The skin drove the geometry, and the structure followed the skin, and then clip was the intermediate. Zahner made notches in the steel, and small cut-outs in the skin for the clip system. There were 100’s of clip types, and 1000’s of clips in total. Each panel had a spreadsheet, and there were columns in the spreadsheet that had. Zahner engineers call this process powercopies. A powercopy is a reusable parametric modeled component. The end result is a face with no face fasteners. Invisible plug welds were used on the front, and rivets on the back.
Zahner strung conduit for the sign and lighting. The signs were placed on the sculptural form before being shipped out. On-site, the final wiring was simply making a connection. The project was installed on site in a matter of days.

Oakley Fifth Avenue in New York City.
Photo © A. Zahner Co.

Oakley Fifth Avenue in New York City.
Photo © A. Zahner Co.

Oakley Fifth Avenue in New York City.
Photo © A. Zahner Co.

Oakley Fifth Avenue in New York City.
Photo © A. Zahner Co.

Oakley Fifth Avenue in New York City.
Photo © A. Zahner Co.

Oakley Fifth Avenue in New York City.
Photo © A. Zahner Co.

Oakley Fifth Avenue in New York City.
Photo © A. Zahner Co.

Oakley Fifth Avenue in New York City.
Photo © A. Zahner Co.

Oakley Fifth Avenue in New York City.
Photo © A. Zahner Co.

Installers lift the Oakley panel on Fifth Avenue in New York City.
Photo © A. Zahner Co.