MOCA Cleveland
The Museum of Contemporary Art in Cleveland
The new Museum of Contemporary Art (MOCA) Cleveland comes from the architects at Farshid Moussavi Architects. The architects designed an elegant prism to house the museum’s collection in a new space that will maximize the 34,000 square foot structure. Zahner was brought on to provide complete facade services for the project, including design assist, engineering, fabrication, and installation of the building envelope & facade of glass and metal.
The design is deceptive in its complexity, appearing at first to be a hexagonal shape. When viewed from above, it becomes clear that the core of the structure is actually 92′ by 92′ cube. This addresses and resolves the common criticism that many of the newer museums with dynamic forms often face — that the space is not actually conducive for the display and viewing of art. This well-thought out museum brings the best of both worlds, with its visually striking design and ample space to display art.
The building’s hexagonal base gives the museum multiple entries, while the building’s square top lends itself to the museum’s rotating collection, allowing the space to be easily divided into flexible temporary spaces. Because the museum has no permanent collection of its own, it was important that the building’s interior lend itself to many different kinds of work.

MUSEUM OF CONTEMPORARY ART (MOCA) CLEVELAND.
PHOTO © A. ZAHNER COMPANY.

MUSEUM OF CONTEMPORARY ART IN CLEVELAND.
PHOTO © A. ZAHNER COMPANY.
Zahner is closely involved with the construction of this shape and surface. Zahner produced a mock-up for the project in June of 2011 pictured below, and will work with the architects to translate the design of this intelligently conceived museum into an efficient and tightly engineered series of components.
TIMELAPSE OF THE MOCKUP FOR MUSEUM OF CONTEMPORARY ART CLEVELAND
FILM © A. ZAHNER COMPANY.
Design Assist for MOCA Cleveland
Zahner provided Design Assist services for the architect. This team of engineers developed the design into a fully defined facade system. The contract entails a design charette, engineering, and a manufactured mockup to test performance details.
This design assist contract enables designers to meet their aesthetic and performance goals, while also working within a prescribed budget. It also puts the owner in control of costs because the entire facade has been defined digitally.
To meet the budget and design constraints required for the project, the team developed a mega-panel; pre-fabricated panels comprised of the finished interior skin, insulation, structure, sheathing, and waterproofing in a single unit.
The Cleveland MOCA’s smart angular design requires a highly engineered and crafted surface. In many ways, the building is as complex to build as some of our more curvilinear projects. The tight corners and edges have acute tolerances, leaving little wiggle room.
During May and June 2011, DAG and Operations teams worked with the architects to produce a mockup. This mockup served as a reference point for the design decisions as the project rolled out into production.

PHOTOGRAPH OF THE MOCA CLEVELAND NEARING COMPLETION.
PHOTO © A. ZAHNER COMPANY.

PHOTOGRAPH OF THE MOCA CLEVELAND NEARING COMPLETION.

PHOTOGRAPH OF THE MOCA CLEVELAND NEARING COMPLETION.
PHOTO © A. ZAHNER COMPANY.

PHOTOGRAPH OF THE MOCA CLEVELAND NEARING COMPLETION.
PHOTO © A. ZAHNER COMPANY.

PHOTOGRAPH OF THE MOCA CLEVELAND NEARING COMPLETION.
PHOTO © A. ZAHNER COMPANY.
The mockup was built to simulate a corner-section at the top of the building. The mock-up for MOCA Cleveland was completed in June of 2011, and a few images of the architects’ visit are featured below.

Photograph of the MOCA Cleveland Mockup at Zahner.
Photo © A. Zahner Company

Farshid Moussavi speaks with Zahner engineers about the MOCA Cleveland Mockup.
Photo © A. Zahner Company
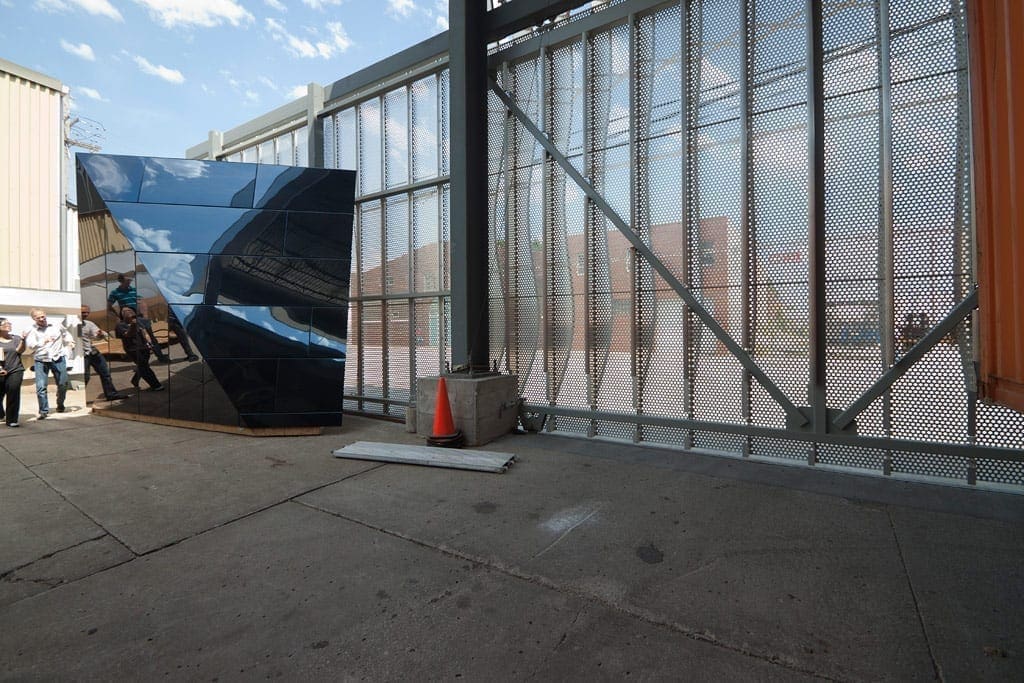
MOCA Cleveland Mockup during the FMA Visit.
Photo © A. Zahner Company

Detail of the reflected sky in the MOCA Cleveland Mockup.
Photo © A. Zahner Company
The material that was selected for this is a seductive dark mirror-polish stainless. Zahner has used a similar finish on a few projects, including a Libeskind-designed residence in the northeast United States. This metal surface is essentially a dark-tinted mirror, reflecting a darker image of its surroundings with perfect mirror accuracy, and imbuing the imagery of the sky and general surroundings on its dark polished surface. The image immediately above shows a detail of the reflected surface of both the inset glazing and the slightly darker reflective metal surface. The Zahner product that enables the flush glass and metal surfaces is called the Inverted Seam™ Glass System.
The building’s upward design was calculated to minimize distraction from reflected surfaces. The design was also tested using computer-modeled simulations of the sun as it arcs across the sky to prevent unwarranted glare and hot-spots.
This is the first museum by FMA, and its first major structure in the United States. Production is slated to begin late 2011, where the operations team and union artisans will begin the process of in-house fabrication and assembly. The custom-designed parts that result from this process are numbered, categorized, and shipped for rapid installation during the final phase of construction on-site. The $26.3-million project is part of a major redevelopment of Cleveland’s uptown area by Case Western Reserve University and MRN, Ltd. as well as others to revitalize the area. The project is managed by Donley’s in Cleveland, and is scheduled to break ground in late 2011.