NASCAR Hall of Fame
NASCAR Hall of Fame in Charlotte, North Carolina
A twisting stainless steel ribbon races around the perimeter of the NASCAR Hall of Fame in Charlotte, North Carolina. Zahner was brought into the project to build the structural form which wraps its facade. The building opened in May 2010, and it serves as a sprawling museum dedicated to racing and NASCAR history.
The building’s design was lead by architect Pei, Cobb, Freed. The firm envisioned a möbius strip-styled stainless steel roadway racing around the perimeter of the main building. The design of a möbius entails the concept of infinity, indicating a sort of infinite path for racing.
To create the building’s möbius required the design of a unique curvilinear shape. To produce this, Zahner engineers implemented the ZEPPS, the Zahner system for building unique architectural forms. Using ZEPPS enabled the architects to design and manufacture the building’s facade efficiently and within budget. It also enabled simple and straight-forward construction of an otherwise immensely complex shape.
The möbius is clad in Angel Hair stainless steel, a product developed by Zahner to reduce the glare and bright spots while providing a satin finish. Even in bright sunlight, the surface has significantly less glare than mill finishes on stainless steel.


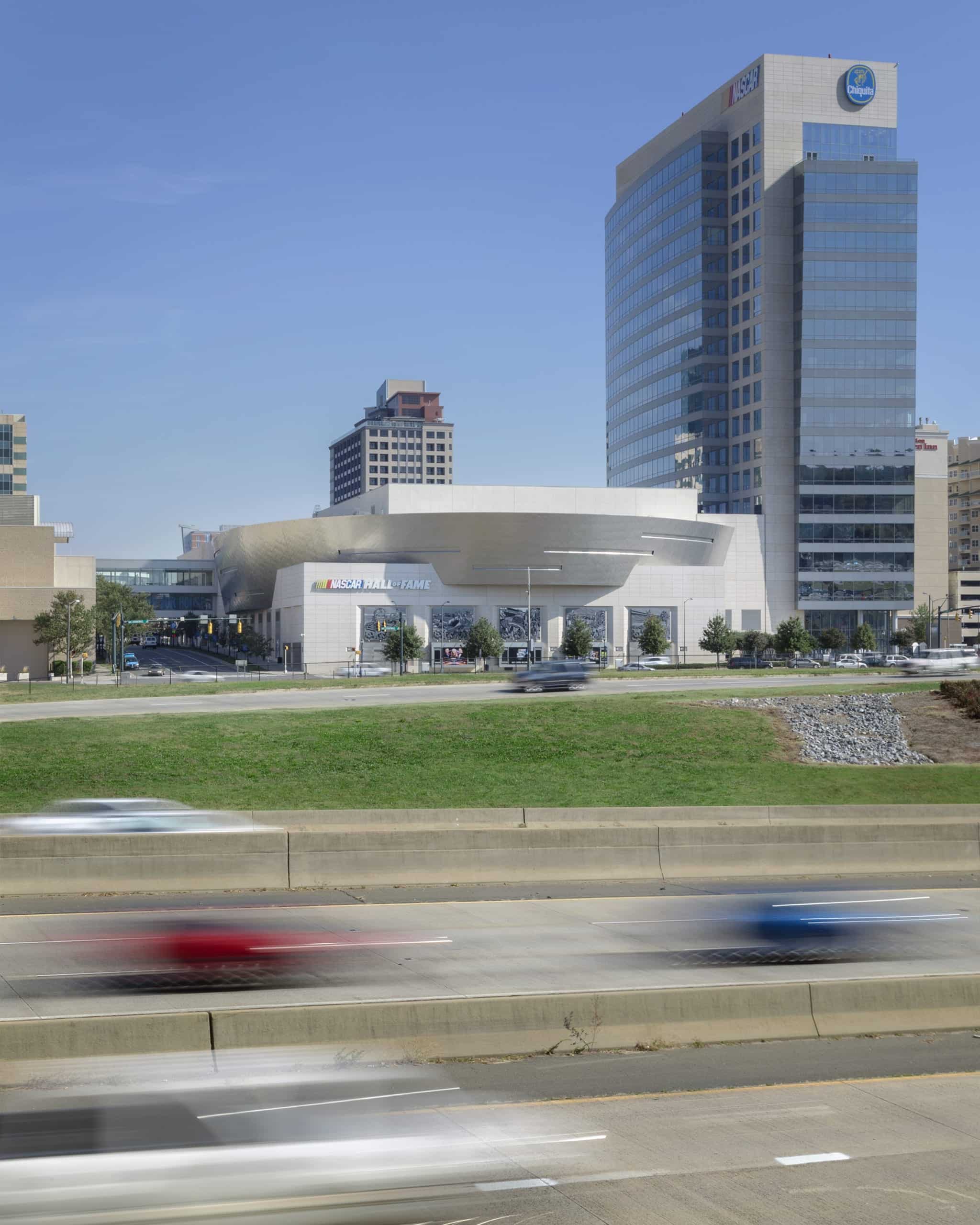
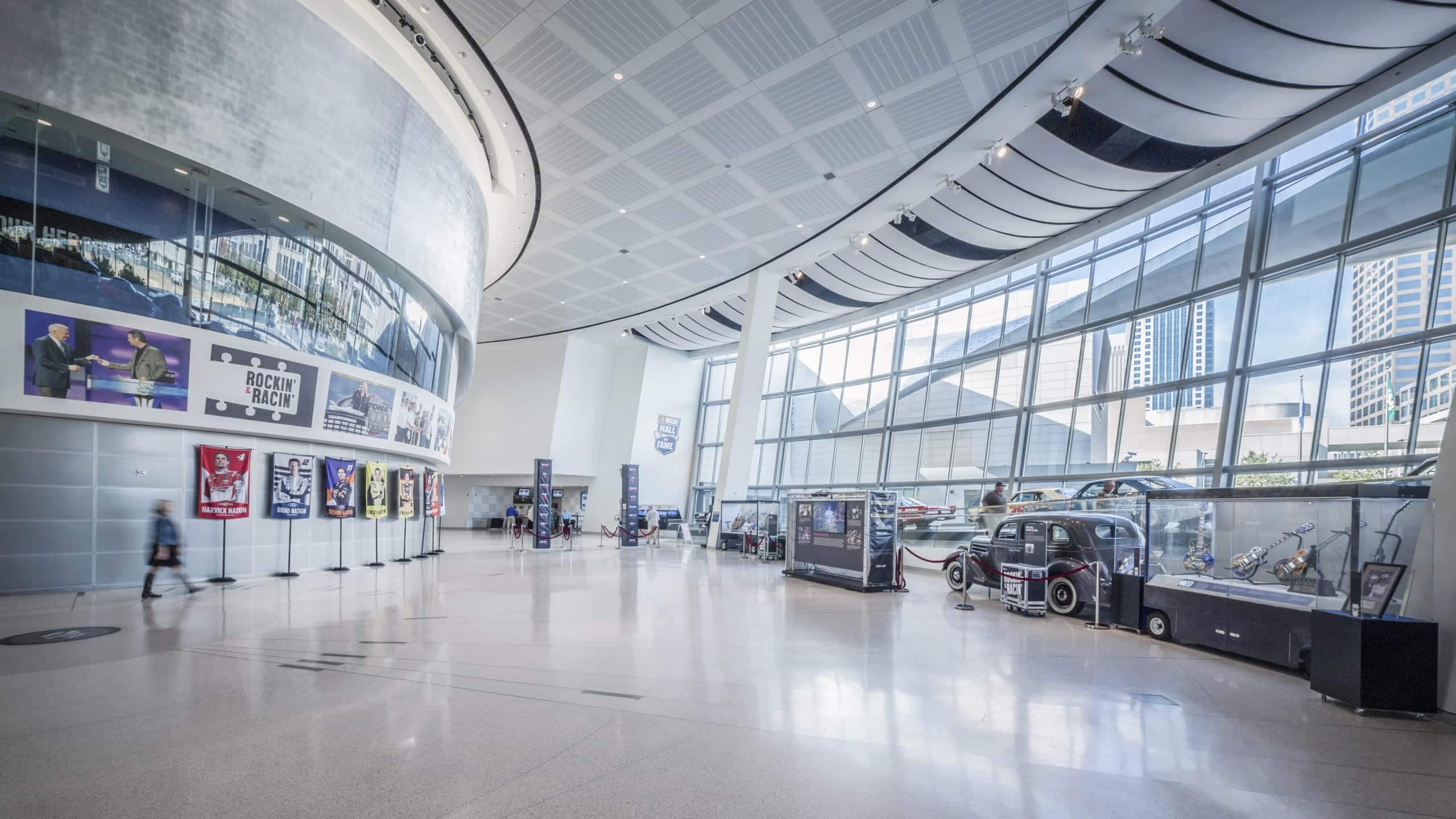

NASCAR Hall of Fame during the day.
Photo © A. Zahner Company


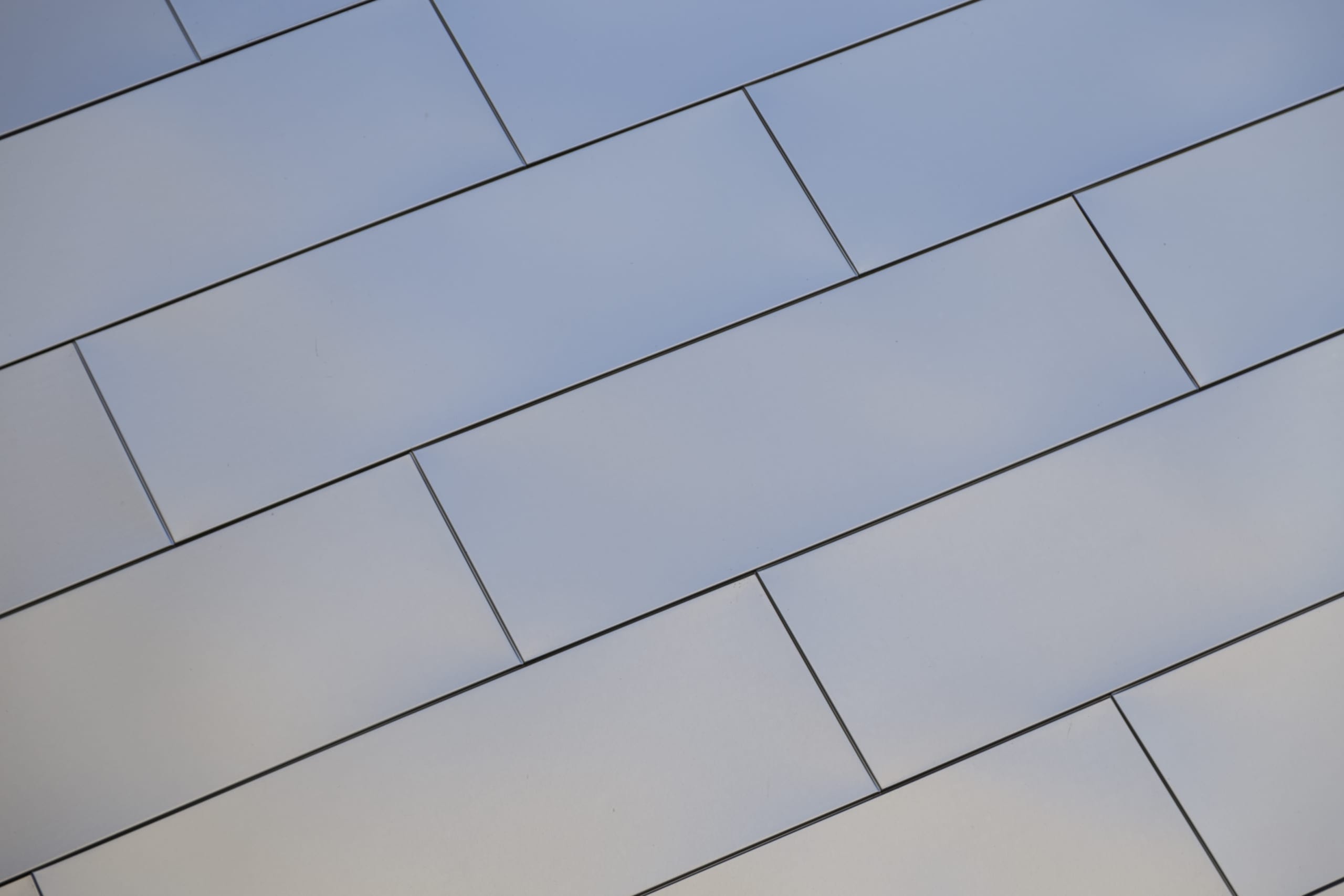
Manufacturing the Unique Facade for NASCAR
The Museum went from design to completion in just over two years. The project’s expedient construction was due to good management by Turner BE&K, as well as a smooth design process.
The design and manufacture of the structural form of the stainless steel was provided by Zahner. Zahner engineers employed a Design Assist method to design the details of the ZEPPS forms.
These ZEPPS forms contain not only the shape and facade, but also electrical, lighting, insulation, and water-proofing. The intelligence of ZEPPS is twofold: you decrease the amount of rigid structural steel which doesn’t like to curve, and you automate aspects of the production of the aluminum forms. In the field, the construction crew receives numbered and pre-assembled parts.
The wall system that makes up the ribbon is constructed from aluminum panels that are approximately 8 foot in width. Wall heights vary with the tallest being in the region of 45 feet. By shipping these forms as preassembled units, the team was able to maximize efficiency in the shop, and maximize efficiency of installing the parts in the field.
“
“Zahner held to our budget, schedule, safety, and quality standards… The ribbon will indeed be the feature remembered by all who visit the NASCAR Hall of Fame. I highly recommend A. Zahner Company for any project which demands the qualities referenced above.”
Tom BarnettConstruction Manager at BE&K Turner Construction.at
A step-by-step process employed by Zahner included the method of splicing plates into specific dimensions and then joined together. Each panel is individually numbered, so construction knows exactly what spliced plate goes between designated panels.

CAD View of the moebius structure Zahner designed compared with the installed view.

Hanging a single NASCAR Hall of Fame ZEPPS Panel.

Detail of the metalwork also provided on the doors for the NASCAR Hall of Fame.

ZEPPS structure that Zahner designed and built for the NASCAR Hall of Fame.
