Irving Convention Center
The Irving Convention Center in Las Colinas
Completed in June of 2010, the project is designed by RMJM + Hillier. The convention center is located in Las Colinas, a master-planned community within the city of Irving, which is itself situated halfway between sister cities Dallas and Fort Worth, Texas.
The project features a Zahner-engineered and produced copper curtain-wall. The entire surface of the project is custom perforated and bumped with a pattern unique to the building. The surface integrates the ZIRA Process for generating the embossed and punched surface.
The surface was installed as mill-finish copper, which means that the raw ‘red’ copper surface will go through a long process of patination. Within weeks of installation, the project had already begun to darken in areas, and within a year, the whole building had a deep bluish brown patina. This natural process is a result of the temperature, moisture, and pollution in the air, which causes the material to at first darken, and eventually change to greens and blues many years from now.
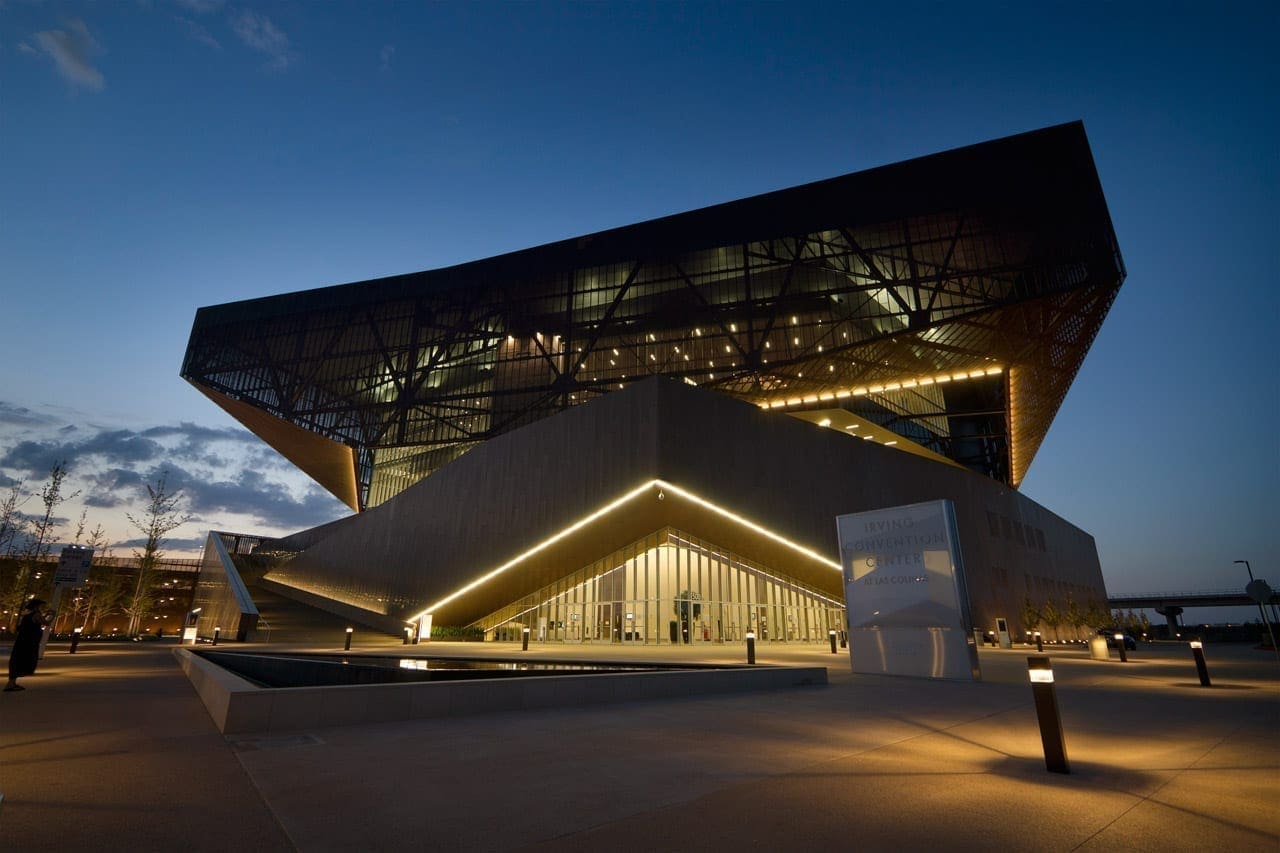
Irving Convention Center (ICC).
PHOTO © A. ZAHNER COMPANY.

View of Downtown Irving from the ICC.

View of Downtown Irving from the ICC.
PHOTO © A. ZAHNER COMPANY.

Irving Convention Center at Dusk.
PHOTO © A. ZAHNER COMPANY.

Irving Convention Center at Dusk.
PHOTO © A. ZAHNER COMPANY.

Irving Convention Center at (ICC).
PHOTO © A. ZAHNER COMPANY.
Achieving LEED Status
In 2013, the Irving Convention Center was awarded LEED Silver status for the built design’s sustainable development. Zahner played a role in ensuring the building’s construction would meet requirements:
- From an operational standpoint, the “stacked” building gains efficiencies with its heating, ventilation and air conditioning (HVAC) systems, translating into a more energy-efficient structure. The vertical plan also meant a smaller footprint of land was needed.
- The copper exterior is more than just a design element. The no-maintenance material translates into lower costs for the center, eliminating the need for painting every few years to maintain its appearance.
- Perforations in the copper skin also provide an important role for energy efficiency, providing built-in shade while using the natural currents of the wind to create a cushion of cooling air between it and the building, decreasing the need for air-conditioning while in essence, shading itself.
- The trusses of the massive 4000-ton steel structure were designed so that they could be sourced domestically; much of the steel came from recycled sources nearby in North Texas and Oklahoma.
Knowing that the pattern would overlap with itself in certain areas, the architects at RMJM Hillier experimented within the bounds of possible perforations to see how two layers of the same material would interact with each other. The result is a smart pattern not unlike the results of moire patterns.
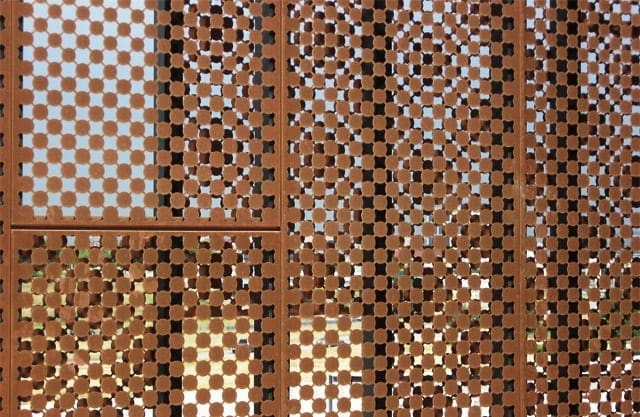
Moire patterns from overlapping perforated metal.
PHOTO © A. ZAHNER COMPANY.

Quatrefoil moire pattern appears in the double-layered perforated metal.
PHOTO © A. ZAHNER COMPANY.
The surfaces above show details of the pattern used and how the frequentoverlaps throughout the project will result in clever patterning. The project was completed in early 2011.
The design is also unique in that at first glance, the material seems impossible. From a medium distance, the metal surface seems to float in space, because the circular shapes are pieced together via slight ‘bridges’ or connecting sections of copper. The effect is that from a near distance, the copper circular sections of the perforation appear to float.