Summer Intern Research
An exciting summer of data visualization and custom robotic fabrication
Summer 2018 was very productive for the Zahner R+D team with two interns joining from opposite ends of the United States. Burcin Nalinci, a Cal Poly/Sci Arc graduate and Michelle Menkiti, an MIT undergraduate, interned between our R+D and Advanced Manufacturing Departments. Their projects,Robot Assisted Welding and Moving Metal, tackled the complexities of manufacturing within the context of mass customization.
Robot Assisted Welding
Human + Robot Collaboration
Welding is a difficult task—comprised of a complex balance of heat, speed, and tacit material knowledge. Zahner utilizes highly skilled craftspersons, some with decades of experience, to create non-repetitive welds of high aesthetic and structural value. In the project Robot Assisted Welding, intern Burcin Nalinci questions whether a collaborative robotic approach to welding could combine the speed and precision of robotics with the knowledge and craftsmanship of our existing welders. Such an approach would both increase what is possible for Zahner to weld while simultaneously removing costly layout and jigging setups required for complex parts.
“
Can a combined human + robot approach to welding streamline the fabrication process of complex assemblies by capitalizing on the strengths of each group?
Video compilation of Robot Assisted Welding project.
PHOTO © A. ZAHNER COMPANY
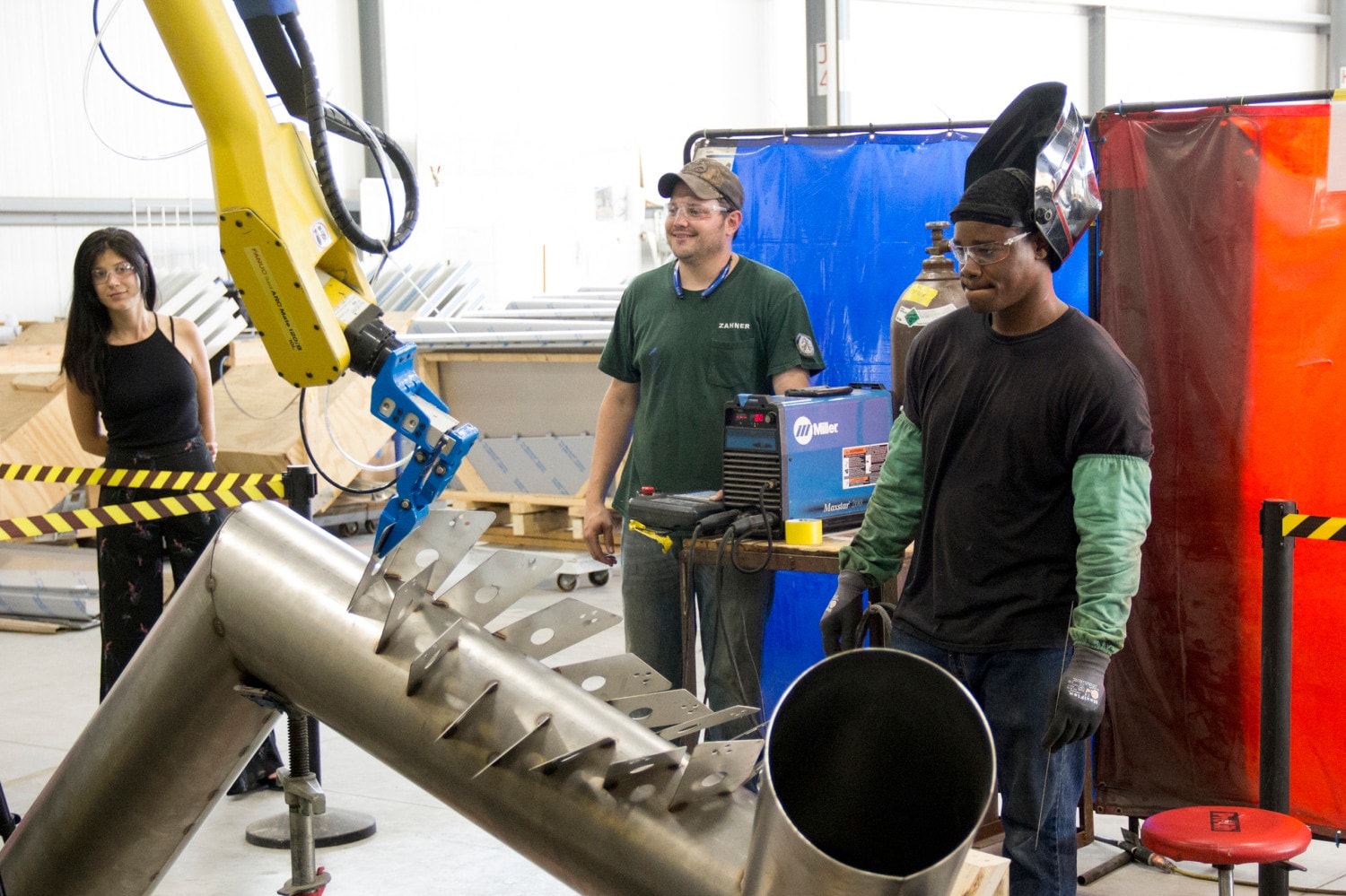
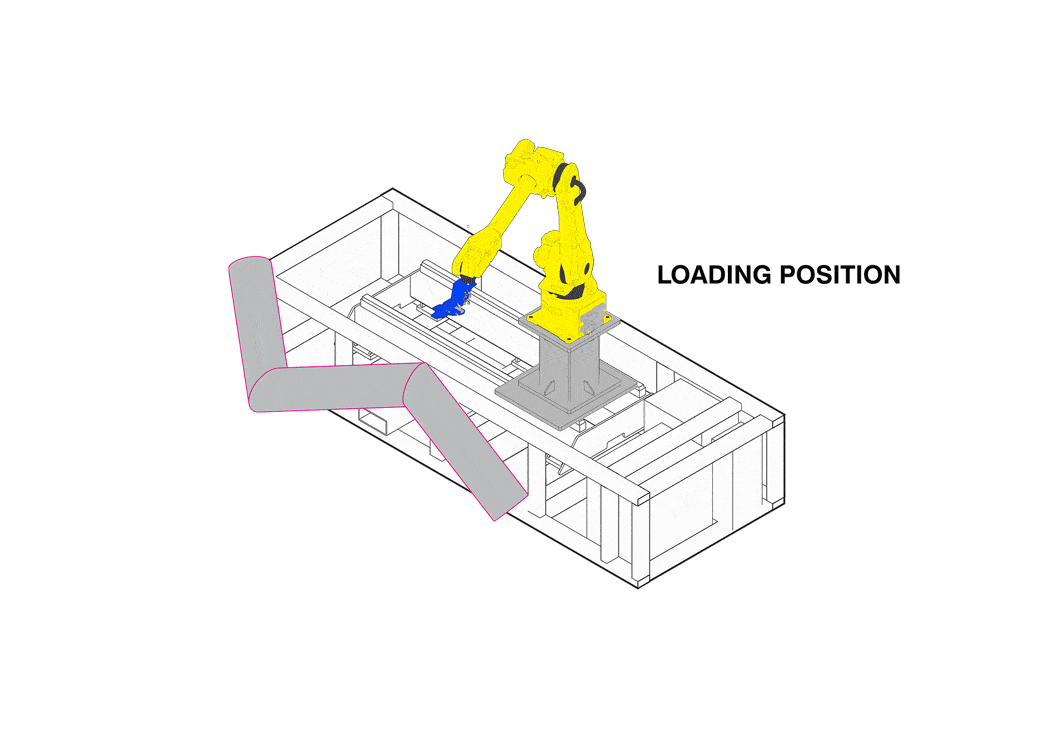
Open Source Gripper
The first project task was giving the robot a means of holding parts for welding. A search for low cost (<$1000) robot grippers proved inconclusive, so Burcin designed and 3D printed an air actuated robot ‘gripper’ for handling parts. Burcin’s gripper tool (end effector) provided over 100lbs of grip strength and cumulatively cost under $100. Burcin found the design so helpful that she published it along with the bill of materials as open source and available here.
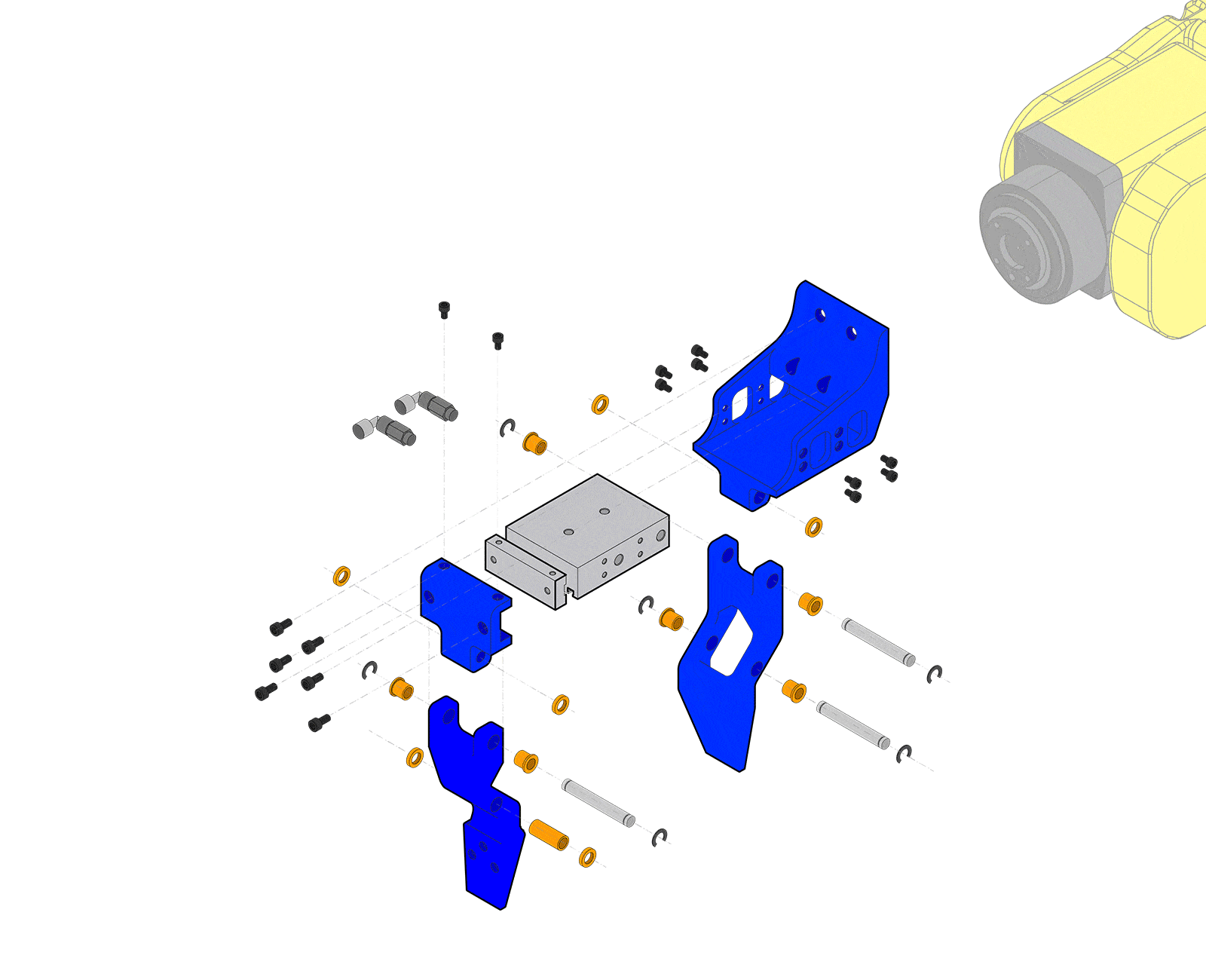

Workflow
Once the robot had a means of holding material, the workflow and respective welder/robot tasks were delimited. The process was a coordinated team effort between a robot operator, a welder, and the robot arm itself.
The operation begins with the robot moving to a ‘loading position’ and opening the gripper, queuing the welder that it is time to load parts. The welder then loads the appropriate part per instructions on the robot teach pendant. After loading, the welder signals the robot that it is time to place the tab. The robot orients the part in the exact location along the pipe and holds it in position during welding. Once welding is complete the welder signals the robot to release the part and return to the loading position. This process repeats until all parts are welded.
Burcin discovered that this workflow removed many traditional engineering and fabrication tasks. No drawings or shop directives were required and no layout, drawing interpretation, or jigging/clamping was required by the welder. Once fabrication was completed, the robot assisted in quality control by conducting a ‘verification pass’, double checking that all parts were placed in the correct orientations. For a place like Zahner that often has 1,000’s of unique assemblies, these savings add up quickly.
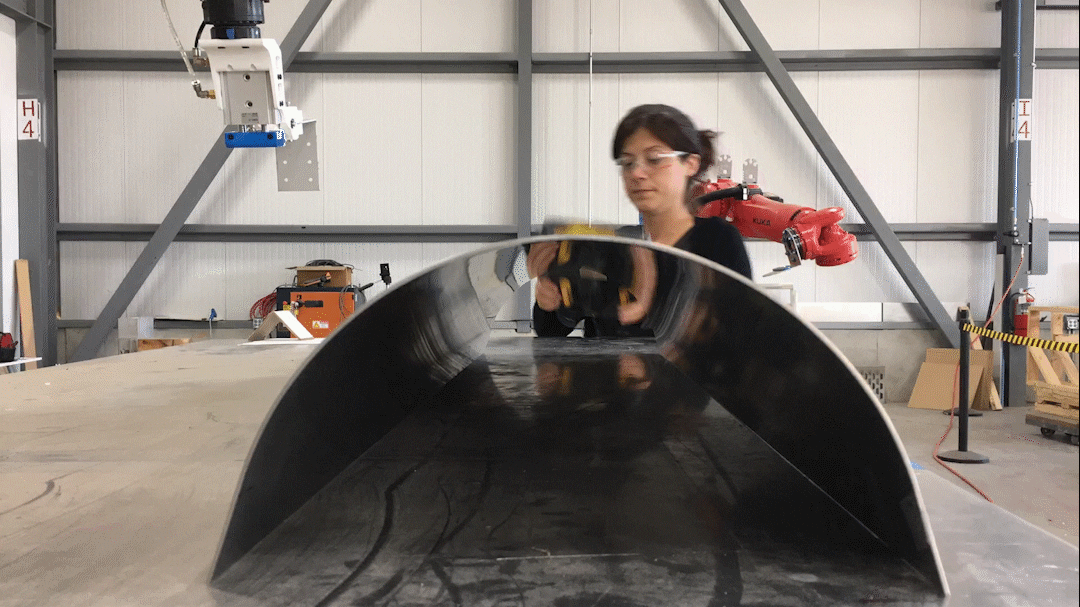
Meeting the Challenges of Mass Customization
One of the challenges of working with robotics on non-repetitive parts is calibration between the physical parts and digital representations. Deviations between the two can cause the robot to crash and/or produce bad parts, neither desirable outcomes. To counter this, a workflow was developed to quickly reorient robot instruction files to coarsely positioned structural pipes so they could quickly be adapted to account for fabrication and positioning tolerances. Simply put, as long as the physical parts were positioned close, the robot could make them perfect without additional engineering.
Each new architectural project presents Zahner with a new and different challenge, we’ve had to develop an agile production strategy to respond to the varying project requirements and ambitions. Robots are flexible by nature, “generalist” machines capable of performing a diversity of tasks. Changing the end effector on a robot immediately changes its functionality while maintaining the same programming logic. Zahner’s R&D group works diligently to increase their fluency in robot programming- making low cost, quick turnaround automation techniques like Robot Assisted Welding possible. This flexible approach to manufacturing further expands Zahner’s fabrication repertoire and in turn what is possible to build.
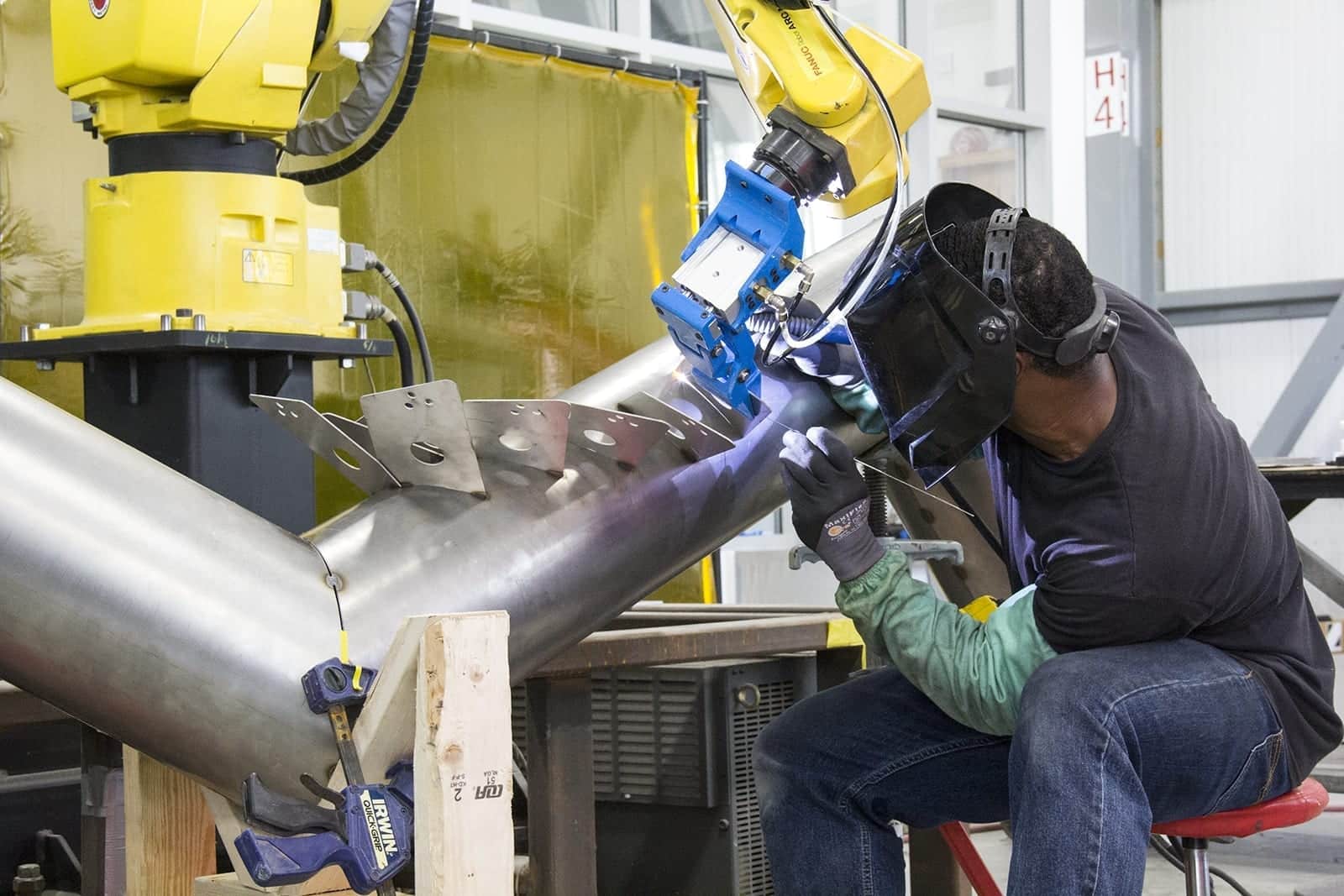
Local 2 Journeyman Keidric Rowe welds stainless steel tab while Fanuc robot holds in position
PHOTO © A. ZAHNER COMPANY

Moving Metal
Lean Manufacturing of Custom Parts
Intern Michelle A. Menkiti, an architecture undergraduate student at the Massachusetts Institute of Technology, joined the team for 10 weeks to delve into and investigate how metals and materials move around the Zahner facilities. With Zahner’s continually expanding work portfolio, and a finite amount of production space, Menkiti’s challenge was to observe current storage and movement methods and then explore ways of improving them. Throughout the summer, Menkiti’s main case study was a 1M+ sqft project in active production—the main question posed to Menkiti was—Where is everything?
At any one point in time Zahner is actively producing 50-80 architectural projects, often composed of tens of thousands of unique parts. Michelle’s project ‘Moving Metal’ targeted the visualization of these shifting entities as both raw goods and finished parts.
“
Where is everything?
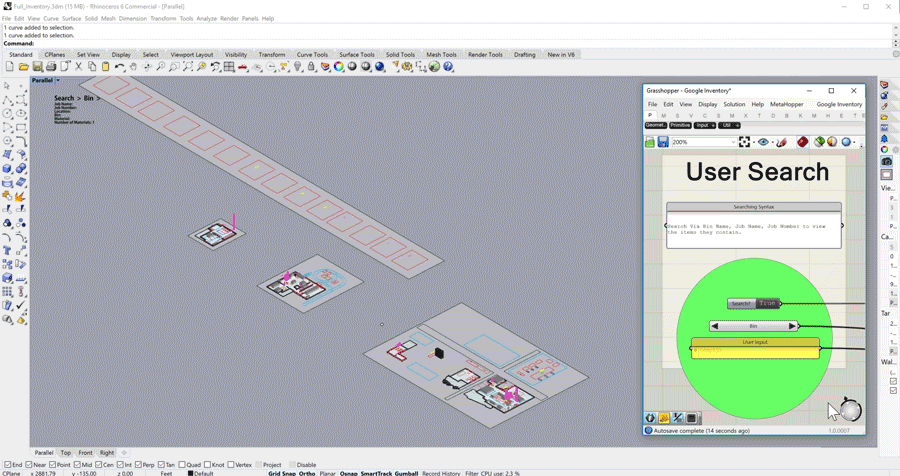
Inventory visualization tool linked to Zahner database
PHOTO © A. ZAHNER COMPANY
To visualize the current state of a Zahner project, data from traditionally separate workstreams needed to be combined. By mapping our inventory database, shipping system, and manufacturing schedule- Michelle was able to generate a company cross section in time. These visualizations were then used as a 3-dimensional diagram of Zahner’s status quo as it changed minute to minute.
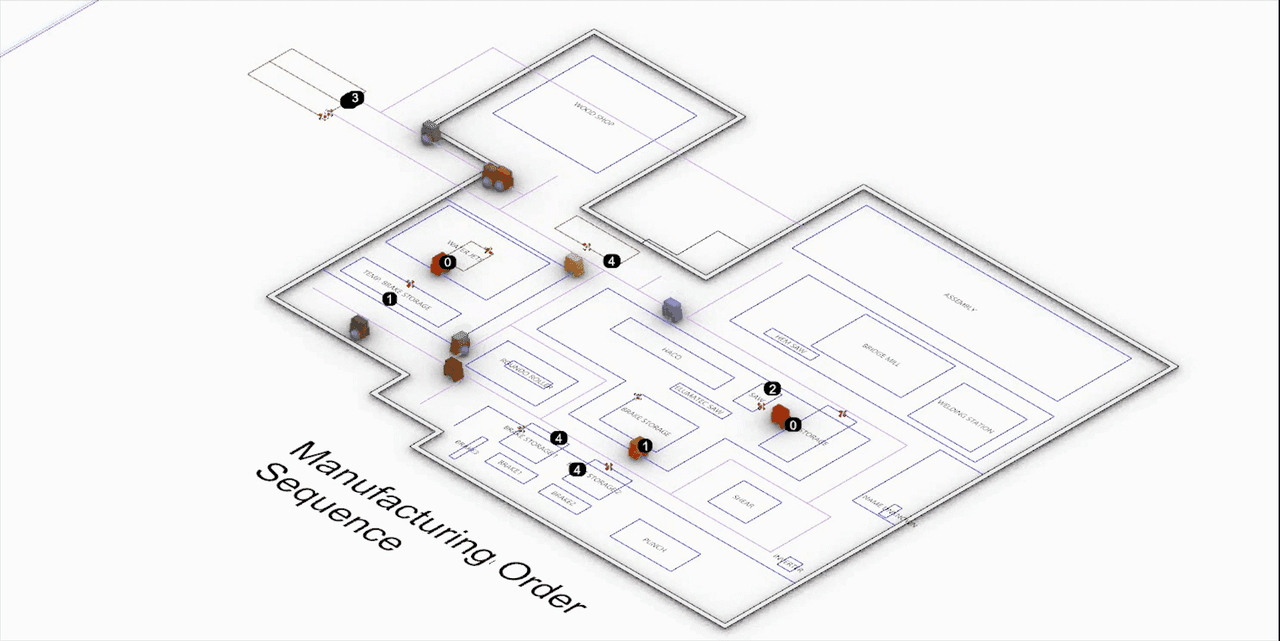
VISUALIZATION OF ZAHNER MANUFACTURING SPACE WITH MULTIPLE SEQUENCED ACTIVITIES
PHOTO © A. ZAHNER COMPANY
Michelle filtered through disparate materials and scheduled production activities by developing tools in Python, Rhino, and Grasshopper. Linked to Zahner’s company database, these tools produced near realtime information on material location, processing information, schedule, and overlapping activities.
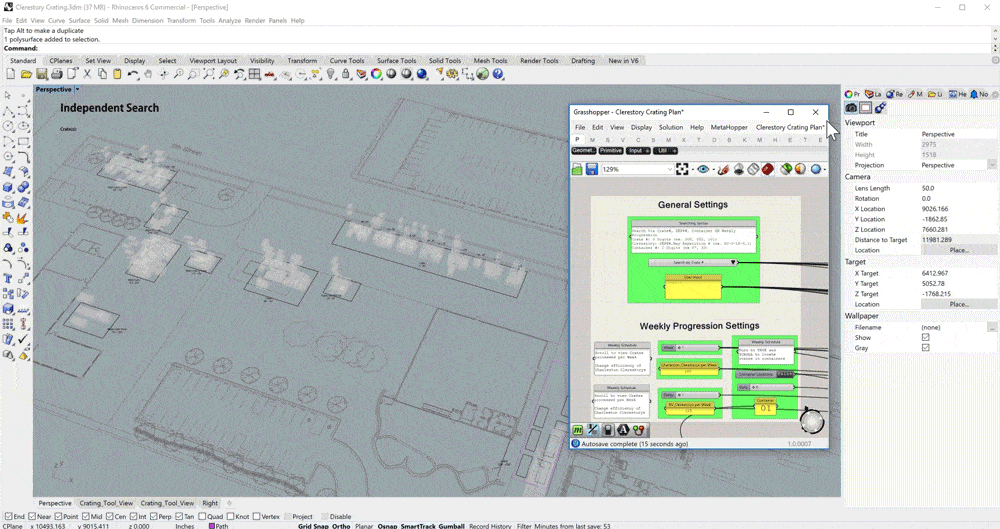
Rhino model driven by shipping and logistics data
PHOTO © A. ZAHNER COMPANY
The tools created for the Moving Metal project helped to improve transparency between Zahner departments, making Zahner more efficient and competitive. Future work will build on Michelle’s proof of concept tools to be utilized by the larger engineering teams.

Pictured left to right: James Coleman (Lead R&D Engineer), Interns Burcin Nalinci and Michelle Menkiti
PHOTO © A. ZAHNER COMPANY