The Fabricator: interviews Zahner
The Fabricator magazine article by Tim Heston describes how complex forms are built by Zahner.
Excerpted from Tim Heston’s article, Fabricating with a Digital Foundation which appeared in The Fabricator.
A shop floor technician at Zahner Co. powers up a laptop – a mundane sight, until you consider what he’s about to view. He opens a dynamic PDF, zooms in, rotates the image, and uncovers cross sections. He’s comparing a part not with a 2-D drawing but with a copy of the original 3-D computer model.
This PDF comes from a solid model that’s part of a building information modeling or BIM, approach the Kansas City, MO., fabricator has been practicing for more than a decade. The model does something many in the architectural world yearn for: to get all parties – the architect; engineers, general contractors, fabricators, specialty contractors, and others – on the same page.
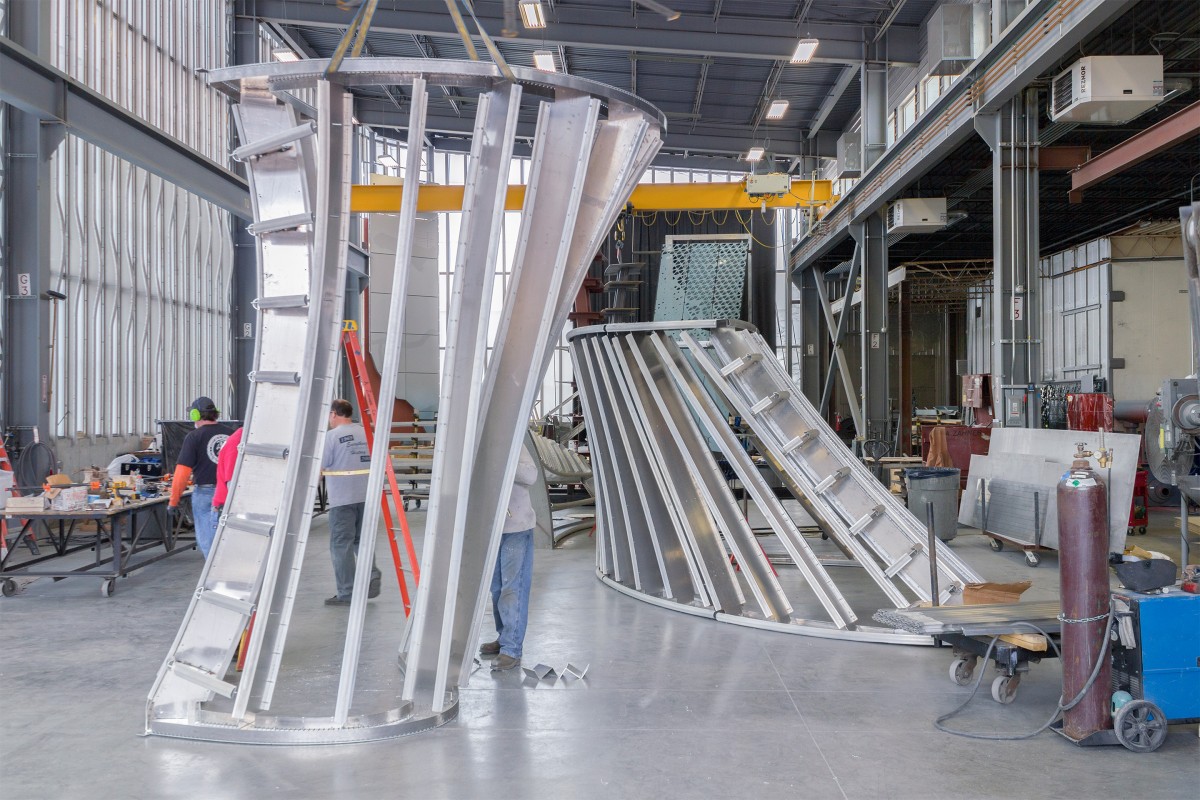
“Before, the substrate would have been built by another company out in the field. Now the substructure is being fabricated here (at Zahner), and because it is, the accuracy we’re able to attain is tremendous.”
Zahner not only fabricates the exterior skin but also the substructure that supports and defines the skin’s complex geometry. This way, the company can be sure the skin fits over the substrate before it leaves the fab shop floor. The substructure usually is made up of aluminum or galvanized material and can vary in depth from a few inches to 5 ft. or more, depending on the project. It can consist of thin layers of material, a series of webs and flanges, or other methods to hold the exterior skin and make it structurally sound.
“Before, the substrate would have been built by another company out in the field,” Robert explained. “Now the substructure is being fabricated here, and because it is, the accuracy we’re able to attain is tremendous.”
Related efforts also involve another first for Zahner: implementing enterprise resource planning (ERP) software to not only manage work orders, bill of materials (BOM), company databases, and other information, but also extend the system’s reach to the company’s on-site work.
“It’s a struggle,” said Robert Zahner, senior vice president, “because we’re not just manufacturers. The ERP system has to go all the way out to assembly in the field. You have piece parts that become an assembly that then gets shipped on-site and installed onto a building. There’s a lot of complexity.”
Read the full article at The Fabricator.