Chrysalis Update
The Inner Arbor Trust Shares Progress on Merriweather Park Pavilion.
This week, the Inner Arbor Trust released an update for the foundation’s upcoming Chrysalis stage, pavilion, and sculpture in Merriweather Park at Symphony Woods. The project is on schedule and being developed by a diverse team working to create a meaningful work of architecture and art for the Columbia, Maryland community. The article below is published courtesy of and with permission from the Inner Arbor Trust
Report on the Chrysalis Development
The Inner Arbor Trust and its world-class team of designers, engineers, contractors and specialty fabricators and installers are moving forward on all fronts in the development of the Chrysalis stage, pavilion and sculpture in Merriweather Park at Symphony Woods; designed by acclaimed and award winning international architect/artist, Marc Fornes, of the New York City based THEVERYMANY.
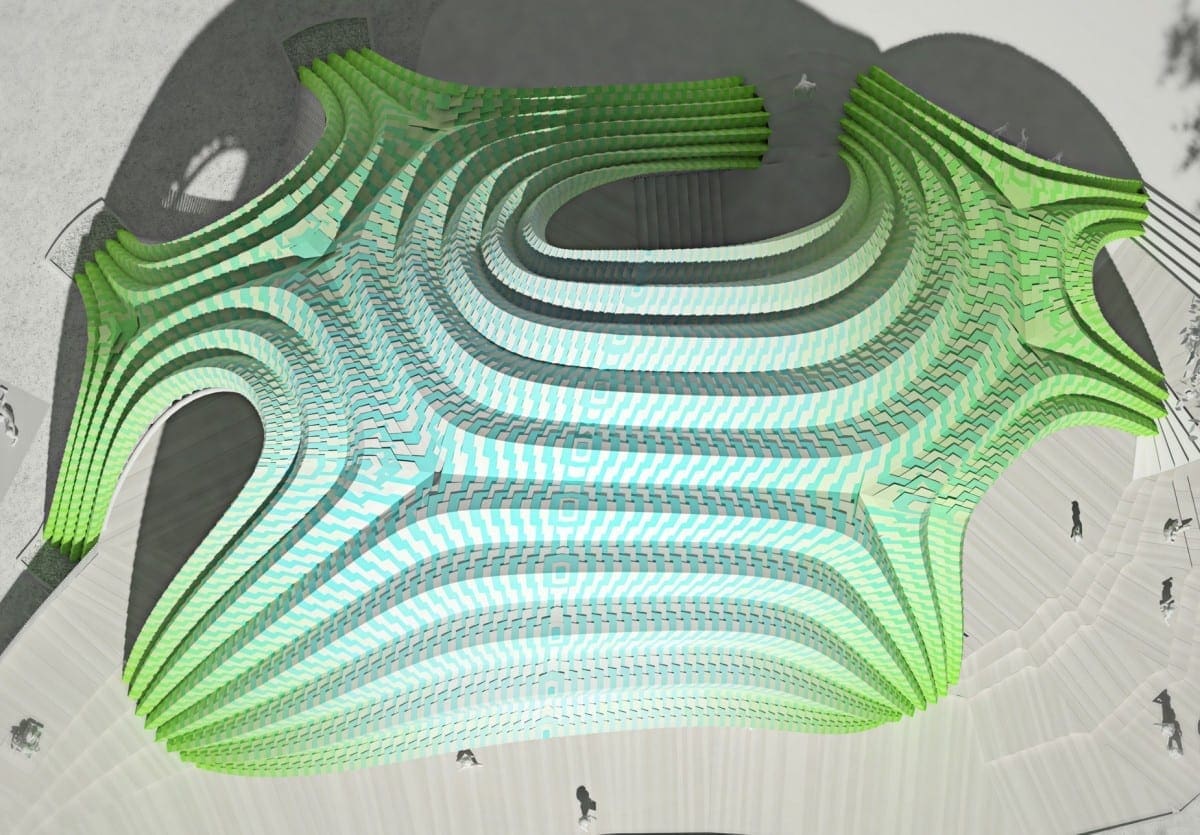
Construction
The Inner Arbor Trust’s general contractor, Whiting-Turner Contracting Company, is rapidly pushing the construction forward. The focus has been on the Chrysalis’ robust Foundation. First, the so called concrete “mud mats” for the Foundation were poured, providing the “foundation” to THE foundation.
Next, the reinforcing steel, or rebar, was formed, placed, tied, and inspected. All the foundation walls have an extensive matrix of rebar; and, the piers, which will directly support the structural steel of the Chrysalis’ canopy, have the most complex rebar configuration and density in the Chrysalis foundation.
Woven throughout the site and through specific areas of rebar are empty utility conduits, placed while the area is open and the walls are still a honeycomb of steel.
After the Washington Post named “Snowzilla” storm, the first major concrete pour of the foundation was successfully made. (See below a picture of the same pier, this time from the inside of the building envelope, and now filled with high strength, 5,000 pounds per square inch, concrete.)
The floor of the Chrysalis will be Ipe wood tiles (for an example, see the following link: Ipe Wood Tiles). Though, underneath the wood tiles the Chrysalis will have a rebar reinforced concrete slab floor, placed at the top of and tying directly into the walls and pier (at the top of the image above, showing the exposed, bent rebar).
What is important to know about the Chrysalis’ concrete floor is that it will form what structural engineers call a “diaphragm,” integrating the vertical foundation walls and piers, with the horizontal floor into a single, strong structural whole. This is the same principle that makes a soup can much stronger with one of its lids fully attached to its cylinder, as the lid acts as a diaphragm, transferring forces exerted from one point, throughout the rest of the can.
The Chrysalis’ strong foundation & floor, designed by the Washington, DC office of the globally respected, London headquartered engineering firm, ARUP is part of the engineering design that allows the Chrysalis – which is shaped like a giant wind catching parachute or sailboat spinnaker – to withstand high winds and support the up to 40,000 pounds of theatrical gear potentially hanging from the Chrysalis steel.
Prior to the structural engineering commencing, in order to guide the engineers, a so called “1,700 year wind event” was simulated in a test on a digitally printed 3D model of the Chrysalis in a wind tunnel at BTM Fluid Mechanics located in London, England.
Steel Fabrication
The steel and aluminum canopy, which will be bolted to the foundation and floor, is the responsibility of specialty design/builder, A. Zahner Company, from Kansas City, Missouri (www.azahner.com). Zahner is renowned for fabricating many geometrically complex special structures, like world famous architect Frank Gehry’s Pritzker Pavilion amphitheater in Chicago’s Millennium Park. (Frank Gehry designed Merriweather Post Pavilion in 1967.)
While the foundation is being built, the detailed shop drawings for the fabrication of the steel “skeleton” super structure, which supports the aluminum “skin,” is underway by Zahner’s subcontractor, Walters Group from Hamilton, Ontario, located outside of Toronto, and its steel erection subsidiary, Metropolitan Walters, located in New York City. Walters is considered to be, “the Zahner of steel.”
The above image is an engineering study computer model of the Chrysalis’ tubular steel super structure. The colors do not reflect the coloration of the steel. All fabricated steel members will be grey, as they will be hot-dipped galvanized for permanent protection against rust.
Walters will deliver the steel on May 15th and immediately commence the erection process. This steel delivery date means that the Chrysalis will be completed this year and its grand opening will be in the spring of next year, in preparation for Columbia’s 50th Birthday celebration.
Aluminum Skin
As the foundation is being built and the steel fabrication is underway, the aluminum skin of the Chrysalis’ canopy is in the final stages of shop drawings.
However, in the context of this parametric design (think algorithms, wikipedia.org), with a complex dynamic form composed of continuously changing compound curves, shop drawings are all contained within Zahner’s state of the art design-to-fabrication computer system and workflow. Zahner uses Dassault Systems’ 3D Experience sophisticated software platform, also used by the likes of Boeing.
This design to fabrication software based workflow is not only the platform in which the structure is modeled, it is also the platform in which, once parametrically designed, every one of thousands of individual and unique pieces is digitally described in instruction sets understood by Zahner’s computer networked and controlled metal cutting, bending and piercing machines. Integral to the design is Zahner’s ZEPPS aluminum truss system, or Zahner Engineered Profiled Panel Systems of aluminum.
In this application of ZEPPS, Zahner is utilizing a cold extruded aluminum “saddle” bracket, which is specifically designed for the Chrysalis project using a custom crafted die, through which the aluminum will be pushed under high pressure, like cold dough through a cookie press, and cut into hundreds of brackets. This saddle bracket takes advantage of the structure’s round tubular steel, which allows each bracket to find its appropriate attachment point on the round steel surface, so as to accommodate the constantly changing angle of the ZEPPS truss system, supporting the aluminum shingles above (see image below).
Schedule & Budget
The one-of-a-kind building will be completed this year, delivering delight to the residents of Howard County and beyond, for years to come.
Critically, the project is on budget, thanks to $6.4 Million in funding from the Howard County government, authorized by the bipartisan support of County Executive Ken Ulman and now County Executive Allan Kittleman; and, the funding was enacted into law by unanimous Howard County Council support, each year for three consecutive fiscal years. Additional funding comes from the Inner ArborTrust’s revenue during the development period.